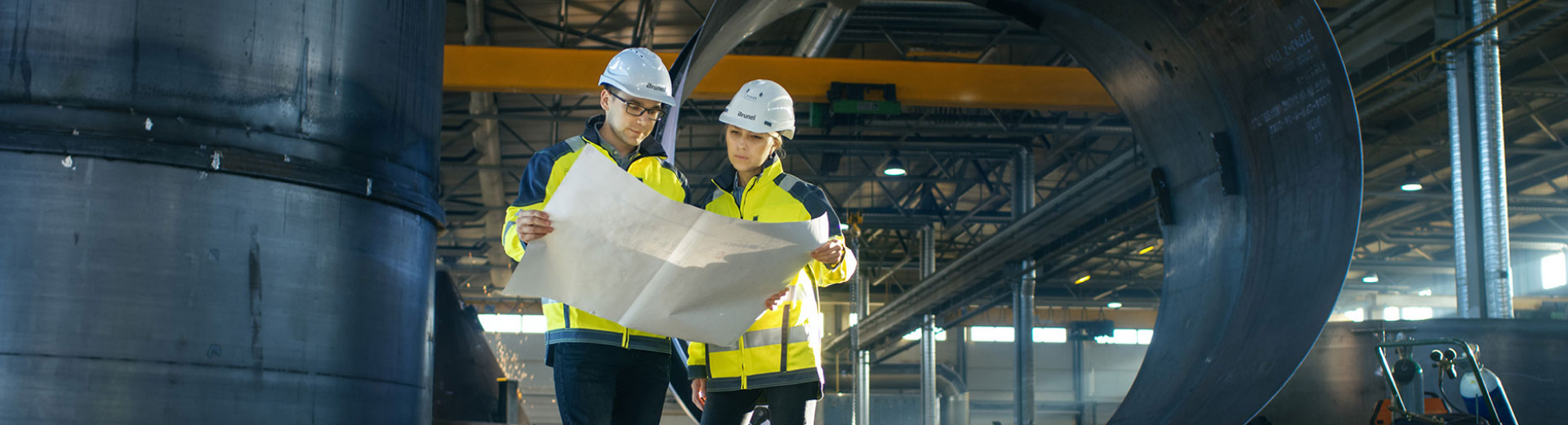
Connecting Specialists to Pioneering Projects
Filters
Country
Australia
69
Papua New Guinea
7
New Zealand
1
Show more
Branch
Infrastructure
28
Mining
20
Conventional Energy
12
Show more
Level of Education
Academic Bachelor
38
Secondary School
15
Vocational School
13
Show more
Total years of experience
2-4 Years
18
Not applicable
17
4-6 Years
15
Show more
Showing 77 search results
Sort by most
12 of 77